Während des Granulierungsprozesses einer Futterpelletmaschine entstehen einzelne Futterpellets oder einzelne Futterpellets mit unterschiedlichen Farben, allgemein bekannt als „Blumenfutter“. Diese Situation ist bei der Herstellung von Wasserfutter häufig und äußert sich hauptsächlich darin, dass die Farbe einzelner Partikel, die aus der Ringdüse extrudiert werden, dunkler oder heller ist als andere normale Partikel oder dass die Oberflächenfarbe einzelner Partikel inkonsistent ist, wodurch die optische Qualität der gesamten Futtercharge beeinträchtigt wird.
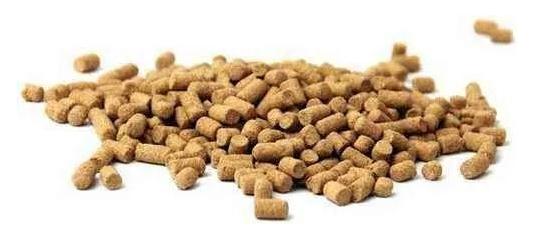
Die Hauptgründe für dieses Phänomen sind folgende:
a)Die Zusammensetzung der Futterrohstoffe ist zu komplex, mit zu vielen Rohstoffarten, ungleichmäßiger Mischung und inkonsistentem Feuchtigkeitsgehalt des Pulvers vor der Verarbeitung der Futterpartikel.
b)Der Feuchtigkeitsgehalt der zur Granulierung verwendeten Rohstoffe ist inkonsistent. Bei der Herstellung von Fischfutter muss dem Mischer oft eine kleine Menge Wasser hinzugefügt werden, um den Wasserverlust der Rohstoffe nach der Feinzerkleinerung auszugleichen. Nach dem Mischen werden die Rohstoffe zur Temperierung an den Konditionierer weitergeleitet. Manche Futtermittelhersteller verwenden ein zu einfaches Verfahren zur Futterherstellung: Sie geben die für die Rezeptur benötigten Zutaten direkt in den Mischer und fügen ausreichend Wasser hinzu, anstatt einen detaillierten und langsamen Zugabeprozess gemäß professionellen Anforderungen durchzuführen. Daher fällt es ihnen schwer, eine ausgewogene Verteilung der Futterzutaten hinsichtlich der Wasserlöslichkeit zu gewährleisten. Bei der Verwendung dieser gemischten Zutaten zur Konditionierung stellt sich heraus, dass sich der Feuchtigkeitsgehalt aufgrund der Effizienz des Konditionierers nicht schnell und gleichmäßig verteilen kann. Daher variiert die Reife der verarbeiteten Futterprodukte unter Dampfeinwirkung stark zwischen den verschiedenen Teilen, und die Farbhierarchie nach der Granulierung ist unscharf.
c)Im Granulierbehälter befinden sich recycelte Materialien mit wiederholter Granulierung. Das granulierte Granulat kann erst nach Abkühlung und Siebung in das fertige Produkt umgewandelt werden. Das gesiebte Feinpulver oder Feinpartikelmaterial gelangt häufig zur erneuten Granulierung in den Produktionsprozess, üblicherweise in einen Mischer oder in einen Granuliersilo. Da dieses Rücklaufmaterial wiederaufbereitet und granuliert wird, kann es bei ungleichmäßiger Vermischung mit anderen Hilfsstoffen oder mit Feinpartikeln aus der Rücklaufmaschine nach der Aufbereitung manchmal zu „Blütenmaterial“ für bestimmte Futtermittelrezepturen kommen.
d)Die Glätte der Innenwand der Ringdüsenöffnung ist uneinheitlich. Aufgrund der uneinheitlichen Oberflächenbeschaffenheit der Düsenöffnung variieren Widerstand und Extrusionsdruck, denen das Objekt während der Extrusion ausgesetzt ist, was zu uneinheitlichen Farbveränderungen führt. Darüber hinaus weisen einige Ringdüsen Grate an den kleinen Lochwänden auf, die die Oberfläche der Partikel während der Extrusion zerkratzen können, was zu unterschiedlichen Oberflächenfarben einzelner Partikel führt.
Die Verbesserungsmethoden für die vier oben genannten Gründe für die Herstellung von „Blumenmaterialien“ sind bereits sehr klar. Sie bestehen hauptsächlich darin, die Gleichmäßigkeit der Mischung der einzelnen Komponenten in der Formel und die Gleichmäßigkeit der Mischung des zugesetzten Wassers zu kontrollieren. Eine Verbesserung der Abschreck- und Anlassleistung kann Farbveränderungen reduzieren. Kontrollieren Sie das Rücklaufmaterial. Bei Formeln, die zur Bildung von „Blumenmaterialien“ neigen, sollten Sie das Rücklaufmaterial nicht direkt granulieren. Das Rücklaufmaterial sollte mit dem Rohmaterial vermischt und erneut zerkleinert werden. Verwenden Sie hochwertige Ringmatrizen, um die Glätte der Matrizenlöcher zu kontrollieren. Schleifen Sie die Ringmatrizenlöcher gegebenenfalls vor dem Gebrauch.
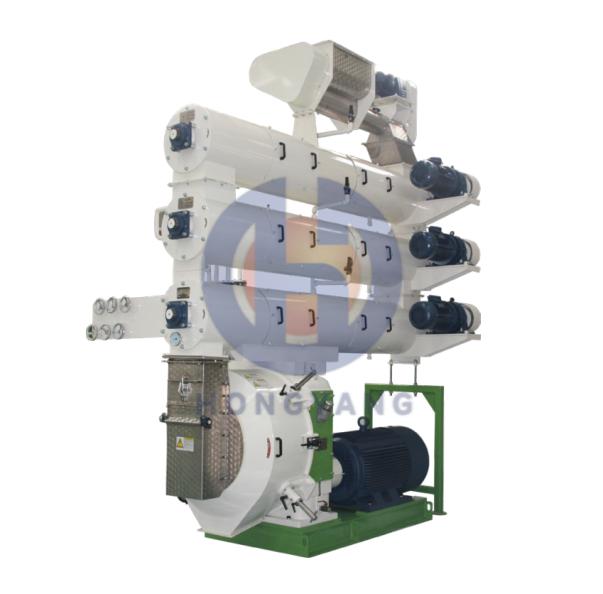
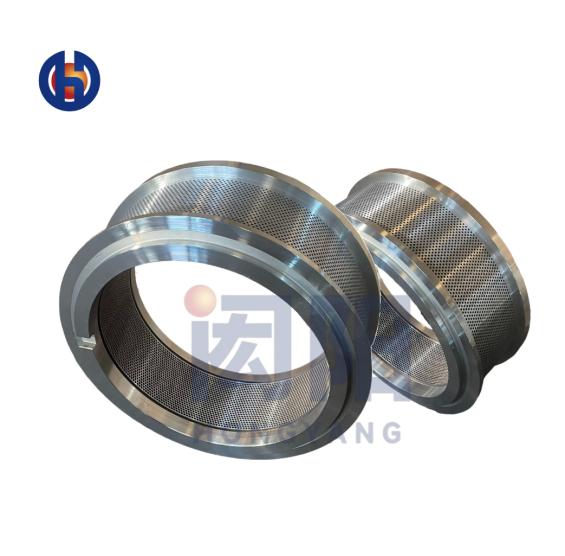
Es wird empfohlen, einen zweischichtigen Doppelachsen-Differentialkonditionierer und einen zweischichtigen Extended-Jacket-Konditionierer mit einer Abschreckzeit von bis zu 60–120 Sekunden und einer Abschrecktemperatur von über 100 °C zu konfigurieren. Das Abschrecken ist gleichmäßig und die Leistung hervorragend. Durch die Verwendung einer Mehrpunkt-Luftansaugung wird der Querschnitt des Materials und des Dampfes erheblich vergrößert, wodurch die Materialreife verbessert und der Abschreck- und Anlasseffekt verbessert wird. Die digitale Instrumententafel und der Temperatursensor zeigen die Temperatur der Konditionierung an, sodass Benutzer sie jederzeit leicht steuern können.
Kontaktinformationen zum technischen Support:
WhatsApp: +8618912316448
E-Mail:hongyangringdie@outlook.com
Veröffentlichungszeit: 26. Juli 2023